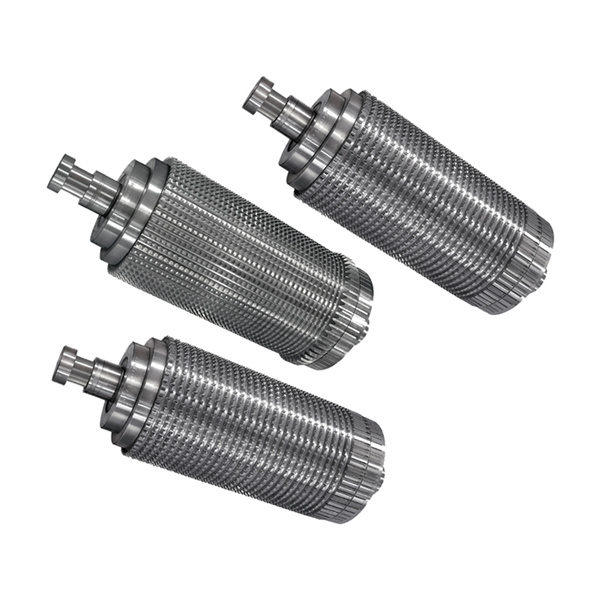
采取拉削方式加工回转体外表面时,拉刀工作原理加工时,工件固定在夹具上随主轴1起高速旋转,拉刀沿工件圆周切线方向作直线进给运动。拉刀的每一个刀齿都可看做1把切向成形车刀。键槽拉刀称由于拉刀各刀齿的切削刃与拉刀支持平面的距离各不相同,当各刀齿顺次切入工件时,从切削刃到工件轴线的最小距离也逐齿变化,从而决定了各刀齿切除金属层的厚度。拉刀可在1次工作行程中完成粗、半精和精加工,且每加工阶段可安排不同的加工余量。 由于工件的径向尺寸由刀具安装位置决定,与进给运动的时间无关,因此加工精度易于保证
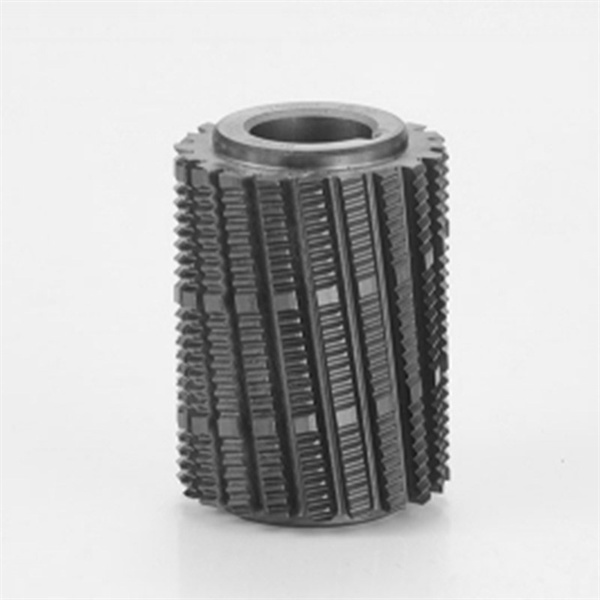
1.各齿前角和刃带宽度保持一致。2.保持拉削过程稳定性,增加同时工作齿数,减少精切齿和校准齿的齿距,提高拉削工艺系统刚性。3.合理选用拉削速度,避免速度过低产生爬行,过高产生振动。4.使用硬质合金拉刀、涂层拉刀、激光强化高速钢拉刀等,这对于提高拉削速度,减少拉刀磨损、提高拉刀寿命和改善拉削表面质量均有良好作用。5.合理选用与充分浇注切削液。
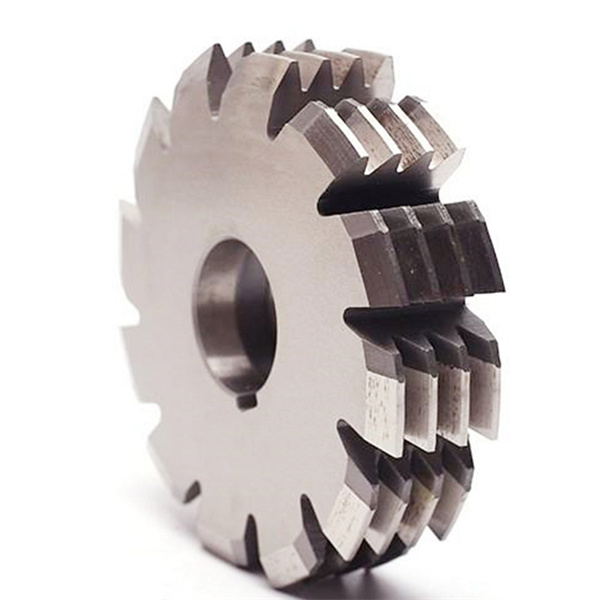
为了消除这种缺陷,从设计方面主要检查齿升量的选定是否合理;同时工作齿数是否太少;刃带宽度是否均匀且偏小等,尤其要着重检查校准部的前七八个刀齿的加工精度。从使用方面看,拉削速度不要过高;拉床的精度与刚度要好,不产生颤动现象;拉刀的弯曲与径向跳动是否超差等。拉刀刃磨:拉刀的磨损主要发生在后刀面上,尤其是在分屑槽的转角处更为严重。